SAFETY SYSTEMS
The study is the first that comes to mind in the security field employee safety. PUSULA Electrical Automation, we are going to do after the risk of damage to your machine and plant workers needed in the analysis of the most appropriate safety system we installed on your system. We made our own in the system as standard and optional security measures to take and we share with our customers.

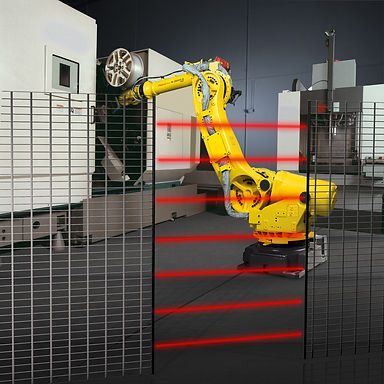
Work safety of the machine-plant to ensure product safety and besides it is necessary to be provided. We neglected this issue frequently, especially if you are sensitive. To know each other, colliding with mechanical components etc .., mechanical measures are taken, even if we are going a step further in avoiding the disruptions that may occur during production as automational taking the necessary measures.
The results of the risk analysis in accordance with the result determined security elements. Where should the light barrier finger, hand, arm, body, chosen differently so as to ensure security. no need to get in place can lead to high costs are very high security measures. The system that needs to be well analyzed.
In surrounded by security fencing system maintenance or door must be kept for use by any other purposes. These doors must ensure that all security conditions required by the system. Safe system automatically stops when the doors opened. In some secure door system it does not open the door. First, the signal is sent to the central controller button to stop the system. When the stance point to stop facility stops the whole system or the relevant departments. From this moment the door is unlocked SAFETY PLC becomes convenient to open the door and mechanically. Pressing the reset button again until the door is closed, the door lock without mechanical lock system certainly work. Although the high cost of this type of security system, controlled safety is working alongside the consideration of the product quality and safety for his stance
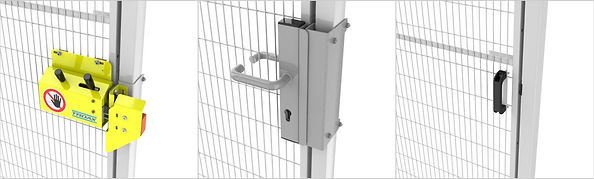

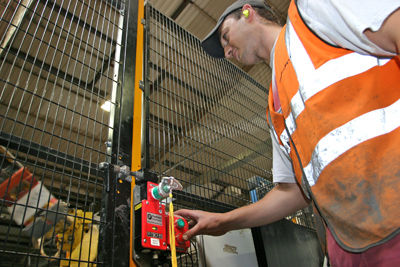

Determining the level of protection required for your facility
Adopt EN ISO 13849-1 has led to new procedural requirements for machine design. The design of a control system safety parts, is a process with several stages of completion.
Defining the requirements of the safety functions
First of all, each safety function must determine the expected properties. This step is the most important and most difficult in some cases. For example, to protect the safety door on a machine, they need to stop the dangerous movement when the safety gate; The safety door is open, the machine must be able to be restarted.
Determination of the required performance level PL
The greater the risk, the control requirements are so great.
Reliability and structure of the additive may vary depending on the technology used. Each dangerous level "a", "e" eating is classified in five stages. PL "a", the contribution of which to reduce the risk control function is low, PL "e" is also high. The required performance level of the safety function described above (PLR) used to determine the risk graph.
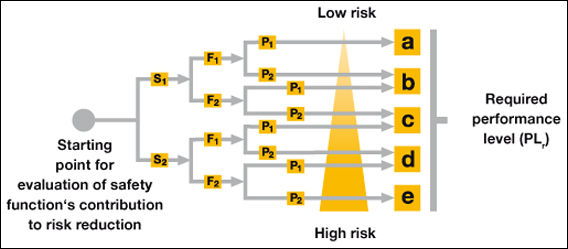
Injury Severity (S)
S1 = Slight (normally treatable) injury
S2 = Serious (normally treatable) injury, including deathFrequency and / or exposure to the hazard (F)
F1 = Rare to very little up and / or short exposure time
F2 = Frequent to continuous and / or exposure time is longPossibility of preventing the hazard (P)
P1 = possible in certain cases
P2 = almost impossible
To carry out the design and maintenance of the safety functions
"security door lock" safety function is performed by control measures. Security door lock, coded as PSENcode be implemented using a zoom switch access. This allows to connect several safety gates in series without reducing the effectiveness of the monitoring function. Coding provides extensive manipulation protection.
Sensors, such as multifunctional PNOZmulti evaluated using a safety system. The drive is switched off using two contactors with positive-guided contacts.
And evaluation to determine the performance level
The safety function is divided into three parts to determine the performance level achieved: input, logic and output. Each of these subsystems contributes to the safety function.
Verification
This step determines the extent to match the level of performance attained the required performance level. Reached PL, PL r required by the risk assessment must be greater than or equal to. This machine design "green light" means.
Confirmation
In addition to the fully quantitative requirements of the safety system it is also very important to avoid systematic failures.
PUSULA service team offers consulting services to help you in each or all six stages mentioned above. Or you want to install the appropriate security systems and commissioning services we provide.


